情熱ものづくりインタビュー
共英製鋼株式会社 枚方事業所
鉄よ、熱く、ふたたび!資源循環型社会を目指してチャレンジし続ける
第12回のインタビューでは、共英製鋼株式会社 枚方事業所のトップ、取締役・常務執行役員の鳴海修事業所長にご登場いただきます。
共英製鋼株式会社は、「一度役割を終えた鉄」を「電気炉」で溶かし、再び鉄製品に蘇らせる『鉄鋼事業』を中核に、さらにその技術を応用して「産業廃棄物を完全無害化」する『環境リサイクル事業』を展開しています。
1947年の創業以来70年超にわたり、鉄スクラップから品質の良い鉄製品を安定的に生産し続けてきただけでなく、社会や自然環境にも目を向け、大きな視野で新たなチャレンジを続けています。
普段なかなか見ることのできない鉄溶解の現場を案内していただきながら、熱いチャレンジ精神はどこから湧いてくるのか、お話を伺いました。
有限な鉄資源を半永久的に
――――鉄資源の循環型を担う鉄鋼事業とは、どのようなことをしているのですか?
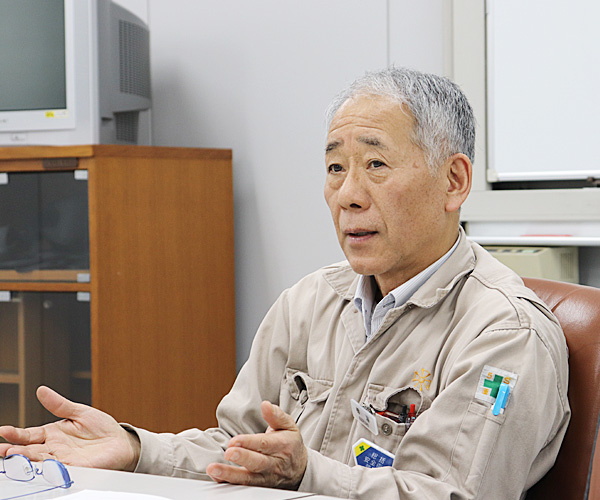
資源が少ない日本で、鉄スクラップは国内で調達できる貴重な資源です。私たちは半永久的にリサイクルが可能な鉄スクラップを原料とし、世の中に役立つ新しい鉄製品に再生するという、資源循環型事業である電炉事業を通じて社会に貢献していきたいと考えています。それは、我が社の経営理念でもあります。
持続可能な社会の構築の一翼を担う企業として、一度役割を終えた鉄を、もう一度利用できるようにするところに大きな社会的意義があります。廃材である鉄スクラップを溶かして新しい鉄製品として提供する電炉事業そのものがリサイクル事業であり、その過程において、省資源、省エネのメリットがある鉄資源循環を我々が担っているということです。
――――鉄資源の循環型を担う鉄鋼事業とは、どのようなことをしているのですか?
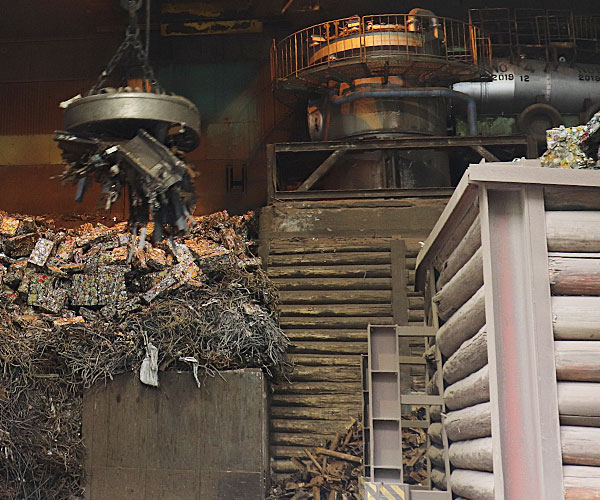
大型クレーンで回収したスクラップを運搬している様子
鉄スクラップとは、身近な物ではジュースの空き缶、ビルや建物の解体で発生する鉄筋やH型鋼、工場で製品を作る時に発生する端材や旋盤屑、そのほか幅広く発生する「一度役割を終えた鉄」を指します。
2017年度時点で、日本国内には実際に使われているものと、スクラップを合わせ約13億トンもの鉄が備蓄されており、備蓄量はなんと世界第3位です。ちなみに、1位が中国で65億トン、2位がアメリカで42億トンとなっています。
枚方事業所では、年間約38万トンの鉄スクラップを扱っています。高炉の原材料である鉄鉱石は輸入することが多いため、ほとんどの鉄鋼業の会社は港のある沿岸部に位置していますが、枚方事業所は内陸部にあり、京都や滋賀、兵庫などの内陸部からの鉄スクラップを集めています。月曜日から土曜日まで、毎日約1,200トン以上がトレーラー等により運ばれてきます。
鉄スクラップを「地産地消」できるのは電炉事業の大きな特徴であり、また鉄スクラップ発生の多い都市部に近い枚方には地の利があると言えるでしょう。
再利用される鉄自体は地産地消ですが、鉄スクラップの価格は国際マーケットで決められるため、国内だけで価格が決まるものではありません。日本での価格が安ければ、価格を維持するため輸出もされます。
――――鉄スクラップから製品ができるまでの工程を教えてください。
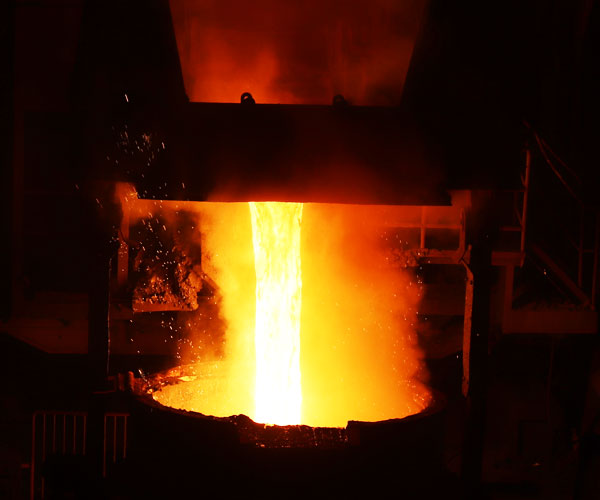
電気炉で溶けた鉄を取鍋に出鋼する様子
枚方事業所には、製鋼工場と圧延工場の2つの工場があります。
まず製鋼工場の電気炉でアーク放電と呼ばれる雷に似たアーク放電を発生させ、その4,000℃~6,000℃の放電熱によって鉄スクラップを溶かします。1回の溶解時(1チャージ)で約100トンのドロドロに溶けた鉄が取り鍋に流れ落ち、その温度は1,650℃にもなります。高温の鉄は燃えて真っ赤というより真っ白な閃光を発し、まさに映画でターミネーターが炉に沈んで溶けていくシーンそのものです。
溶けた鉄はやがて四角い棒状のビレットと呼ばれる鋼片となり、圧延工場に運ばれて行きます。
何度も何度も圧延機の中を連続して加工され、徐々に細くなっていき、最終的に1本が80mの細い棒状の製品(枚方事業所では直径10mm~16mm)になります。その工程はそうめんづくりと似ており、そうめん束のようなお客様の扱いやすい棒鋼製品づくりを目指しています。
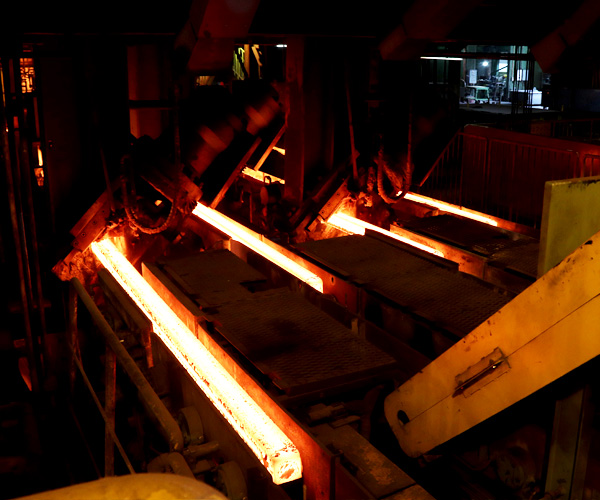
溶解された鉄はビレットに成型されます
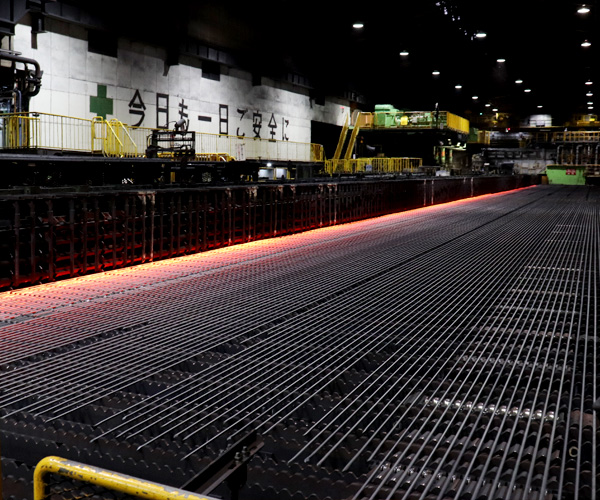
圧延工場で加工される棒鋼
培った技術力で、多種雑多な素材を均一製品に
――――なぜ電気炉を使って鉄スクラップを溶かすのですか?
鉄を溶かす方法には高炉法と電炉法があります。高炉では「鉄鉱石」と呼ばれる鉄分を豊富に含んだ鉱物を、石炭やコークスを燃焼還元させて溶かすことによって鉄を生産します。電気炉では、電気のエネルギーを利用してスクラップを溶かし、鉄を再生しています。
高炉と比較して電気炉はCO₂の排出量が少なく、設備の規模が比較的小さく済みます。エネルギー消費量が少なく環境にやさしいと言えますね。それに、製品化する際の注文に合わせて少ロットで多品種の生産にも適しているなど、とても柔軟性があります。
――――鉄スクラップはいろんな不純物が混ざっていて、製品化は難しいのでは?
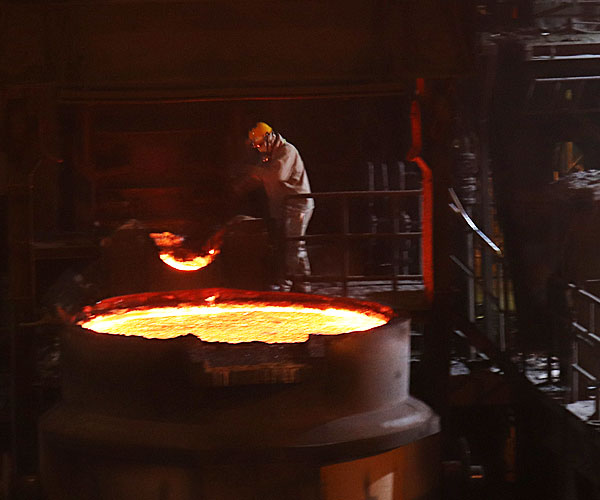
高温の鉄の入った取鍋から成分確認のサンプルを取る様子
製品の仕様は決まっていますが、原料となる鉄スクラップの成分や形状が一様でないため、1チャージ毎に分析して、成分の配合を調整していかなければなりません。マニュアル通りにやっても成分を一定に保つことは非常に難しく、高品質の製品を安定的に生産していくためには長年の経験と技術力が必要なんです。
技術者は、料理人みたいなものです。腕のいい料理人は肉や魚や野菜などその日仕入れた素材を使って、メニューに載った美味しい料理を作り続けます。経験豊富な技術者も多種雑多の原料で、いつも均一のものに仕上げていきます。これは技術者にとって腕の見せどころで、一番おもしろいところなんです。
――――どのような製品に生まれ変わっていくのでしょうか?
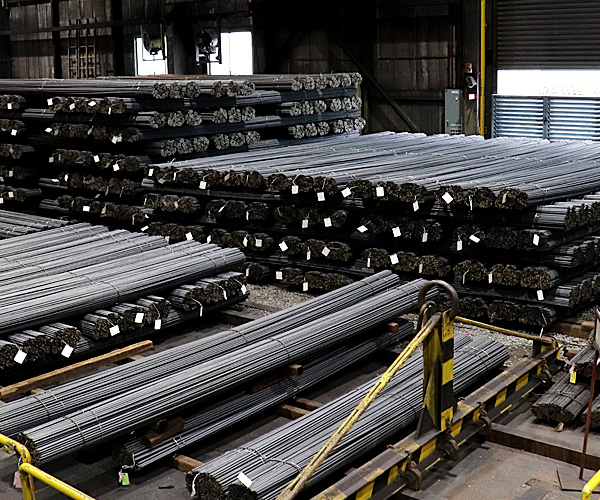
枚方事業所で製造した鉄筋
共英製鋼グループとしては、建築などに使われる鉄筋コンクリート用棒鋼をはじめ、平鋼、等辺山形鋼、ねじ節鉄筋、Iバーなど、多種多様なものを製造しています。平鋼は船舶の材料、等辺山形鋼は駅のホームの屋根や、高圧電流の鉄塔の一部に利用され、Iバーは溝蓋の材料として利用されます。
枚方事業所では主に、鉄筋を製造しています。 主力製品である鉄筋は建物の土台部分として利用されています。また、クレーンのフックやボルトの材料などに幅広く使用されている丸鋼の製造も行っています。
――――その高い技術力を活かして、電炉事業の海外展開も早くからされていますね。
1973年に日本の鉄鋼業として初めてアメリカに進出しました。また、ベトナムにも日本の鉄鋼業として最初に進出するなど、グローバル化の先駆けとなり、これまでにブラジル、カナダ、イタリア、タイなど20か国以上の国で技術指導や経営指導を行ってきました。現在はベトナムに3か所、アメリカに1か所の事業拠点を有し、ベトナムの空港やカンボジアの鉄橋など、途上国の発展に必要な社会インフラを支える仕事をしています。
電気炉のアーク熱を利用した環境リサイクル事業
――――産業廃棄物を完全無害化する「環境リサイクル事業」のパイオニアだとか?
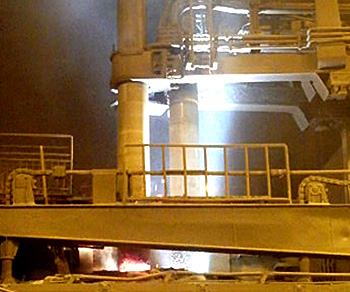
電気炉は稼動時に4,000~6,000℃のアーク熱が発生
鉄スクラップを溶かす時、電気炉には4,000~6,000℃のアーク熱が発生します。この熱を有効利用しようという発想からスタートしたのがわが社の環境リサイクル事業です。
種々雑多な素材が混在する産業廃棄物を安全かつ適正に処理するには、綿密な管理と確かな技術が必要です。わが社では、早くから産業廃棄物処理を手掛け、そのノウハウを蓄積してきました。
山口事業所では、有害物質である医療廃棄物の完全無害化を日本で初めて行いました。処理の難しい注射針やメス、手術の際に発生する感染性の医療廃棄物を安全かつ適切に完全無害化する処理方法を独自に開発してきました。
産業廃棄物の中には、水銀や代替フロンなど、人体や環境に有害な物質が含まれていることもあり、そのまま破棄できないものもあります。こうした廃棄物も超高温の電気炉で一気に溶融することで安全に無害化でき、CO₂の排出量削減に繋がり、カーボン・オフセットにも貢献しています。
――――環境への意識の高さは、周辺地域の環境保全にも繋がっているのですね。
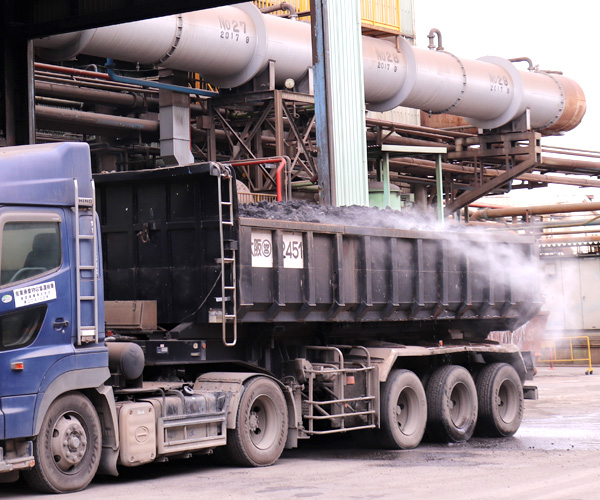
スラグ(トラック上)と集塵ダクト(トラック上部後方)
地域社会の環境への配慮は徹底してやっています。わが社のコアビジネスが、鉄スクラップを製品に再生するという資源循環型事業ですが、その過程で環境保全のための様々な工夫を行っています。
鉄スクラップは同じように見えても、成分が全部違うんです。カーボンの含有量が異なったり、メッキしているものがあったり、不純物も多く含まれています。それら鉄スクラップを溶かす時に出るニオイや煙などが外へ出ないように集塵機で除去していますし、超高温になる設備を急速冷却した冷却水もそのまま外へ出さずに再利用するなど、厳しい管理体制を敷いています。
また工場で発生した「スラグ」と呼ばれる鉱さいは道路を作る時に必要な路盤材として有効利用され、廃棄するものはほとんどなくゼロエミッションを志向しています。
地域密着から最先端技術まで、枚方事業所の取り組み
――――社員寮が近くにあり、遠方の出身者も枚方に住んでいるそうですね。
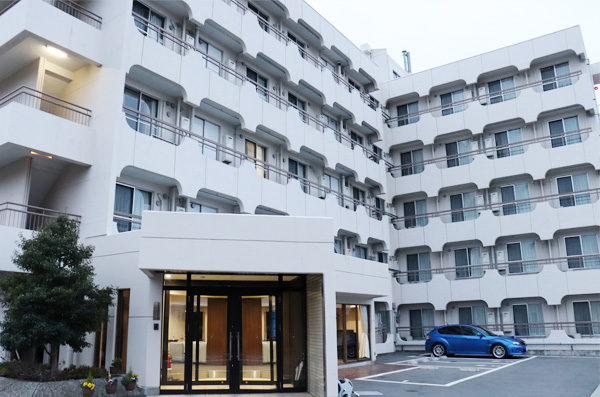
寮は以前からあったのですが、4年前の耐震強化を機にリニューアルし、ワンルームマンションのような綺麗な個室に改装しました。現在は30名ほどの寮生が暮らしています。朝夕2回の食事が付いています。「新築マンションみたい」「栄養バランスのとれた美味しいごはんが食べられる」「職場に近く、居心地もいいので、安心して仕事ができる」と寮生に好評です。
――――工場見学の受け入れを積極的に行っているとお聞きしました。
1月には枚方市が支援する「枚方子どもいきいき広場」の子どもたちが見学に来て、迫力ある製品づくりに目を輝かせていました。これからの時代を生きる子どもの「生きる力」を育んでいこうという活動に参加できたことは嬉しく思います。
枚方事業所は1971年に操業を開始した歴史ある工場です。同業の海外企業への技術支援・指導を行ってきた経緯があり、多くの優れた技術者を生み出している伝統ある事業所です。地域の方々にもっと身近に感じてもらうために、その一環として工場見学を積極的に行っています。
――――現在、そして今後の枚方事業所の取り組みについてお聞かせください。
現在、「労働生産性向上」をテーマに働き方改革を実施しています。事務所側では月に4回ノー残業dayを設定し、残業時間の短縮に努めています。
今後、工場内では電気炉前にロボットを導入し無人化を図ることで、これまで人が実施してきた危険な作業をロボットが行うようにします。また、新しく建てる倉庫では自動化を実現させて安全に効率よく製品を仕分けし、出荷できるようにしたいと考えています。
次世代へつなぐチャレンジ精神
――――創業者・高島浩一氏は「常にチャレンジする人」であったそうですが、その志はどのように受け継がれているのでしょうか?
高島浩一は、事業拡大や利益の追求でなく、戦後荒廃した日本を、日本人をもう一度世界に認めてもらいたいという想いを大変強く持っていました。社員に対しては「できぬできぬは工夫が足らぬ」と、そういうことを言い続けて「一番になるために何をするかということを考えろ」と言い続けてきました。そうしたチャレンジ精神は、現 高島秀一郎会長を筆頭に、さまざまな形で当社の若い人たちに受け継がれています。
取材にご協力いただいた社員の方々
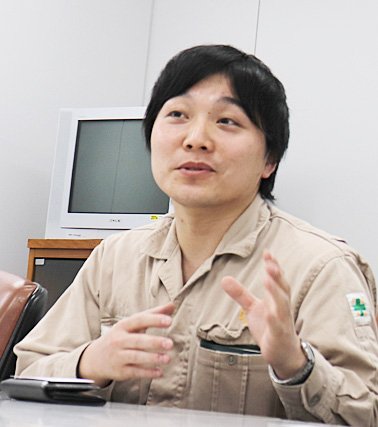
◆製造部製鋼課 小川 卓也 さん
入社10年目。入社して4年目にベトナムでの勤務を経験。2年4か月の間、現地子会社の技術指導などにたずさわりました。「ベトナムは日本の20年前の国と言われていましたが、実際は最先端の技術を取り入れていました」と、ベトナムの技術力の高さに驚いたそうです。
「これからは鉄だけに頼らず、それ以外のものを発案してみたい。チャレンジして失敗しても、次に活かせるように温かい目で見守ってもらえるので、自分で工夫してチャレンジでき、やりがいがあります」と、力強く語っておられました。
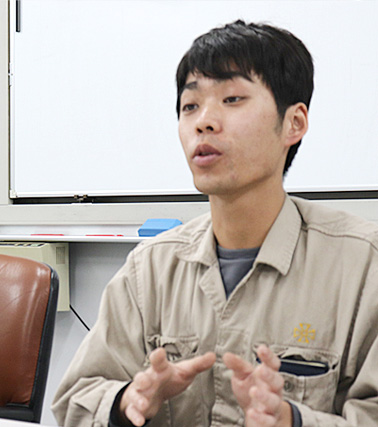
◆製造部工務課 松比良 亮 さん
入社3年目。大学では電気工学を専攻し、プラズマを用いた鉄鋼材料について学んだ。「卒業したら“鉄”に関わった仕事をしたい」というのが、この会社を選んだ理由だったそうです。
「入社してすぐに大きな仕事をやらせてもらいました。責任ある仕事を任せてもらってありがたいです。これからも失敗を恐れず、やってみようと思っています」と、意欲満々です。
「常にチャレンジする人」であった創業者・高島浩一氏の志は、時代を経て、人を経ても、ここ枚方事業所の若い世代へと着実に受け継がれています。鉄を溶かす超高温の熱にも負けない熱いチャレンジ精神は、これまでも、これからも、共英製鋼の大事な財産であると感じたインタビューでした。
また、三露 正 業務部長には、事前準備から当日の工場撮影、インタビューまで、大変お世話になりました。電気炉の鉄溶解は電力需要が少ない夜間や土曜日に行われるため、撮影可能な時間帯が限られています。社員の方々は各持ち場でシフトを組んで業務にあたられています。そんな中、撮影のタイミングや社員の方々のインタビュー時間の調整など、柔軟に細やかに対応いただきました。ご協力に感謝いたします。